Established in 1968, VEEM Ltd began as a small engineering services company, specialising in the repair and dynamic balancing of drive shafts, engines and other rotating equipment.
Over the years, the proud family business has been led by two generations of the Miocevich family. The name VEEM was formed from the initials of the founders Voyka and Elizabeth Elsie Miocevich.
By the late 1980s, VEEM Ltd won its first major defence contract for the manufacture of submarine valves for the new Australian Submarine Program under licence from Flowserve Defence UK. Some 30 plus years later, VEEM Ltd is still manufacturing these safety critical, submarine hull valves – a testament to its focus on quality control and engineering excellence. Another major milestone saw VEEM Ltd acquire two highly specialised non-ferrous foundries and eventually integrate them onto one site in Canning Vale, Western Australia.
In the 1990s, VEEM Ltd built a strong partnership with Austal Ships and became the supplier for hollow bronze castings for its aluminium ships. This relationship continues to this day. As VEEM Ltd grew, the directors realised that VEEM’s engineering services was limited by the physical boundaries of the Western Australian marketplace and to be successful globally, the business really needed to expand to not only manufacture bespoke equipment for others, but to become a manufacturer of its own technology and products.
Recognising the growing global market demand for high performance marine propellers, VEEM Ltd began developing a ground-breaking propeller manufacturing technology to target this highly specialist market segment. VEEM Ltd became the industry expert manufacturer with superb design, ground-breaking technology and associated patents, plus the most advanced CNC machinery and robotics worldwide. A strong, global distribution network, a highly advanced Internet portal and full production tracking capability for clients, were additional highlights of this modern global product.
Building upon its core strengths in the fields of technology and precision engineering design, in 2012, VEEM Ltd commenced development of a range of powerful gyrostabilizers for super yachts, patrol boats and offshore working vessels. These gyrostabilizers were developed for use on large boats and small ships operating in very demanding commercial applications. With an unwavering passion for beautiful design and engineering excellence, VEEM Ltd launched a market-leading product in 2015 that dramatically reduced the rolling motion of vessels, increased at-sea time and improved personnel safety. The 6 model range represents the largest size of powerful, high quality marine gyrostabilizers in the world.
Today, VEEM Ltd is a leading manufacturer of disruptive high technology products for the marine, aerospace, defence, oil and gas industries. Based in Perth, Western Australia, VEEM Ltd operates from a 14,700 sqm purpose-built fabrication and manufacturing facility, including Australia’s largest non-ferrous foundry.
The Complete VEEM Ltd History
1968 – Commencement of VEEM
In October VEEM Engineering Services commenced trading as a partnership between
Voyka and Elizabeth Elsie Miocevich at 14 Whyalla Street Willetton.
The business was established to carry out Dynamic Balancing services and Drive shaft re-manufacturing. These services were steadily expanded to cover a range of repair machining services, heat-treating and the manufacture of a small metal turning lathe.
1976 – Death of founder
In February 1976 Voyka (Charlie) suddenly passed away. The business employed twenty-two people and was placed in the care of employed management with Elizabeth over seeing the business.
1982 – Takeover by current Directors
Late in 1982 there was a recession in the Engineering industry which caused VEEM to reconsider its management structure. The business was taken over by Gary, Mark and Brad Miocevich, the sons of the founder. There were then fourteen people employed by VEEM.
1987 – Quality System Accreditation
As VEEM grew and started to take on more oil and gas and defence related work it became apparent that a quality system would be required to develop the business to maximise the market opportunities. VEEM was the first company in Australia to achieve accreditation with no major non-conformances and was one of the first accredited companies in Western Australia.
1988 – Commencement of ERP system
In an effort to better manage production VEEM embarked on a custom written ERP system. The system covered labour collection via bar coding on each job and computerised purchasing enabling a completed job cost report to be printed for all jobs. Job costing and customer details were able to be stored on computer for future reference.
1989 – SS Engineering
SS Engineering was a non-ferrous foundry that manufactured a range of marine propellers and provided non-ferrous castings to industry. The business had been owned for a number of years by a group of investors and had been poorly managed since the retirement of its long serving manager Ron Morrison. VEEM had the opportunity to purchase SS Engineering which was about to play a significant role in a large contract VEEM had secured to manufacture submarine hull valves. SS Engineering was one of only two significant non-ferrous foundries in Australia.
1989 – Premier’s Award for Excellence
VEEM won the inaugural Premier’s Award for Excellence in Industry and Technology, which was recognition of the unique high quality defence work VEEM had brought to Western Australia, VEEM’s advanced computerised ERP system and VEEM’s performance in achieving AS 1822 quality accreditation.
1994 – ABE framework adopted
Following intensive studies of Baldridge award winning companies in the USA, VEEM elected to adopt these principles which were developed by Demming, and others in Japan, as part of the US rebuilding program after the Second World War. Australia’s adaptation of these principles is the Australian Business Excellence Framework. VEEM adopted this as its management model to encourage a sustainable management system for the future.
1995 – Management Restructure to integrate SS Foundry and VEEM Corp
VEEM Corporation owned both SS Engineering and VEEM Engineering. The finance and administration function was carried out in VEEM Corporation. This structure was not ideal and was changed so that all finance and administration functions as well as SS Engineering were integrated into a renamed VEEM Engineering Group.
1997 – Commencement of TSA
As part of a business planning process VEEM searched the world for a suitable gas turbine maintenance partner. Thomassen International proved to be such a partner and a company was formed which was jointly owned by Thomassen International and VEEM Engineering Group. This company was called Thomassen Service Australia Pty Ltd (TSA). The aim of this company was to provide GE frame type gas turbine maintenance services previously unable to be performed in Australia. This business concluded in 2005.
1998 – Relocation to Canning Vale
By 1998 VEEM had outgrown its existing facilities and employed around 90 people. It was decided to relocate all three facilities, two in Willetton and one in Welshpool, to a new larger site in Canning Vale. The new site featured 25 tonne overhead cranage throughout and had around 5500 sqm of floor space. The site has been widely recognised as the premier engineering facilities in the state.
2000 – Management Restructure to create the Commercial Division
To take advantage of the efficiencies offered by having all divisions of the company on one site, the company split into Commercial, Production and Finance and Administration divisions. This restructure enabled VEEM to concentrate on marketing the business more effectively to industry and increase its market share.
2000 – Upgrade of ERP system
Although VEEM had added many modules and reporting functions progressing into the initial ERP system, there was still a need to upgrade to a windows based system and to pursue other strategic objectives. In 2000 VEEM embarked upon a major upgrade of the ERP system to include areas such as intellectual property management, quote and job control by operation bar codes (as against general job card bar coding), paperless purchasing and debtors system, scheduling and production control monitoring. The operating system was upgraded to Oracle to allow search engines to be used.
2001 – IPS workshops
VEEM reached an agreement to take over the mechanical workshops operated by IPS at the Western Power premises in Kewdale. VEEM employed many of the staff and also purchased key equipment. By applying the VEEM ERP system VEEM was able to turn this work into a profitable part of the business. This relationship was also the springboard for the working relationship created between IPS and TSA to jointly work in the gas turbine maintenance industry in Australia.
2001 – Exporting propellers to the USA
As VEEM had developed sophisticated designs for a range of propellers and enjoyed a low Australian dollar, VEEM decided to market its marine propeller range into the USA. This was very successful with the VEEMSTAR – C proving to be the best high-speed propeller on the market. This led to a continually increasing amount of orders originating from the USA.
2002 – Exporting Controllable Pitch Propeller Components
Through a MJP Waterjets agency, VEEM was also able to commence exporting controllable pitch propeller components to Sweden. The components were cast hubs of up to 3 tonne for large frigates. Europe had a shortage of high quality non-ferrous foundries and Australia’s low dollar placed VEEM in a very attractive position.
2002 – Acquisition of Timcast
The purchase of VEEM’s major competitor Timcast, allowed VEEM to combine the complimentary resources of both companies in copper and nickel alloy melting technologies. Timcast performed similar bronze sand casting to VEEM, as well as a unique centrifugal casting process of hollow bars. This proved to be a very successful acquisition.
2002 – Manufacture of Components for Large Hadron Collider
Delivery was made of large cast and machined components for the Hadron Collider under construction at the European Organisation for Nuclear Research (CERN) high energy particle accelerator. The components manufactured from a lead bronze alloy were cast, machined, tested and trial assembled prior to delivery for installation. The components made up key elements of a radiation shield to protect instrumentation to be used in the ATLAS experiments being designed to uncover fundamentals questions of physics to advance the understanding of the deepest laws of nature. The Hadron Collider confirmed the existence of the Higgs boson particle in 2012.
2004 – PowerPlay Research and Development Project
The PowerPlay project commenced following a successful submission with the government Start Grant Program. This allowed the development of a range of propellers that became very successful in the US and European markets. The project developed a state-of-the-art design and manufacturing system. Some of the key features included:
- Web based propeller-ordering system.
- Software to manage automatically created propeller geometry and tool path data.
- Acquisition, installation and development of 5-axis CNC machining capability giving VEEM the unique ability to fully machine propellers in one set-up.
- Acquisition, installation and development of robot sand machining capability. Advanced robotic technology has been lodged for patent protection which enables VEEM to manufacture infinitely variable propeller castings to an accuracy not seen before in the industry.
- Acquisition and commissioning of a high-powered 64ft Viking test vessel that allows the testing and data collection of propeller design iterations.
The outstanding success of the PowerPlay program resulted in the decision to make propeller marketing and manufacturing a key business feature of the future company direction.
2005/6 – New workshops
The acquisition of Timcast had resulted in the outgrowing of the 1998 constructed workshops. A new factory to house 5 axis CNC machines was constructed. A new foundry was also constructed to combine the existing Canning Vale foundry and the operations at Osborne Park. The combined floor space of the new and existing factories became approximately 10,500 sqm. The new workshops provided state-of-the-art facilities in foundry, sand recycling, centrifugal casting, fume extraction, metal melting, and associated processes. The operations at Osborne Park were discontinued and all operating processes relocated to the new Canning Vale facility.
2006 – Interceptor Project
Investigations were made into the viability of an Interceptor style propeller being released to the market. The investigations included preliminary proof of concept trials, manufacturability trials and market acceptance research. The outcome was favourable and this resulted in the decision to invest in the research, development, and commercialisation of a range of Interceptor propellers. The project was conducted between 2006 and 2010 whereby an integrated and automated system to manufacture propellers using Interceptor technology was developed.
2007 – Lodgement of Patents for Interceptor
Patents applications were lodged to protect the intellectual property relating to the Interceptor propeller design. This included the proposed groove and strip design as well as the application of a nickel coating. This advancement has cemented VEEM Propellers as the world leaders in commercial mono block propellers.
2008 – Establishment of VEEM Ltd
In 2008 it was decided to change VEEM Engineering Group from a proprietary tmited company to publically unlisted company to allow for easier potential capital restructure in the future.
2009 – Strategic Marketing Model Development
In response to the structural changes to Australian industry brought about by the GFC and higher Australian dollar, VEEM developed a new business operating model based on selecting potentially larger product or service volume targets. These targets could offer volumes large enough to justify the necessary research and development expenditure to significantly increase their profitability
2010 – Supacat UK announces support contract with VEEM
Supacat UK announces that VEEM will become its Australian service partner on the new Nary high mobility vehicle being supplied to the Australian SAS. The contractual arrangements between Supacat and VEEM is considered by the Department of Defence is considered to be revolutionary is it allows local support services via their LPO system, but comes with full OEM approval. This allowed fast and OEM approved repair of the Nary high mobility vehicle deemed as critical by the SAS.
2011 – Acquisition of Halcyon assets for VEEM Gyro
After studying the stabilization market for some years, VEEM Ltd decided to develop a range of gyroscopic ship stabilisers. This was specifically identified as a product that could meet the company’s key criteria of:
- Advanced technology
- IP protection
- Company manufacturing capability
- Marketing within existing framework
- Meeting financial risk profile
2011 – Development of the ‘Forever pipe’ range of wear pipe.
VEEM Ltd developed a bi-metal bar that is centrifugally-cast and has a wear-resistant inner pipe cast inside it during the manufacturing process. The new pipe was estimated to extend the life of wear pipe by 6-10 times that of traditional wear pipes at 10% less cost. Wear pipe is used extensively in the mining and mineral processing industry. VEEM recognised an opportunity to develop the next generation of wear pipe.
2012 – Fast Loop Manufacturing
The implementation of a semi automated fast loop manufacturing process into the foundry, enabling castings smaller than 1.4 m to be manufactured far more efficiently. This was recognised as being particularly valuable for the manufacture of propellers, as it significantly offsets the impact of the high Australian Dollar.
2012 – 4 year LCS contract secured
Commencement of production on the next 8 ship sets of the mechanical components for the Littoral Combat Ship manufactured by Austal Ships. VEEM successfully secured the contract to manufacture 2 ship sets of ride control components per year for 4 years.
2013 – Supacat awards VEEM $3mil contract
Supacat awards VEEM a $3mil contract to perform a major upgrade on the 31 Nary high mobility vehicles. This contract is to bring the vehicles to the necessary configurations and strength specifications to withstand the vigorous demands of the Department of Defence.
2014 – ASC award partnership contract with ASC
Australian Submarine Corporation awards VEEM the first of a new generation of partnering contracts for the Collins Class Submarine. VEEM is embedded into ASC South Australia operations and the Submarine stores are relocated to VEEM in Perth.
2015 – Market release of new VEEM Gyro stabilization unit an achieves first sale
After four years of exhaustive research and development and engineering design, VEEM releases the first of three VEEM Gyro modes, the VEEM Gyro 120. The first unit was sold and will be despatched March 2016.
2015 – VEEM Gyro 120 and 260 enter production
Due to the positive market reaction VEEM commenced manufacturing the 120 and 260 model gyros. Ten of each unit are commenced through the VEEM global supply strategy. They are due to be completed progressively through 2016/2017 financial year.
2015 – 3 year LCS contract secured
Commencement of production on the next 6 ship sets of the mechanical components for the Littoral Combat Ship manufactured by Austal Ships. VEEM successfully secured the contract to manufacture 2 ship sets of ride control components per year for 3 years.
2015 – Supacat appointed VEEM as an Australian partner on the Redfin 1B
Supacat appointed VEEM to participate in the Australian build program of the Redfin 1B high mobility vehicle (similar to the Nary). This is a $2mil contract for the manufacture of 18 chassis to ‘the waterline’ level, so that they can be driven. Final assembly is carried out in Sydney by others.
2016 – VEEM releases a range of Conquest Propellers
VEEM developed a series of propellers under a new brand, Conquest Propellers, targeted specifically at the global replacement propeller market. These propellers are available anywhere in the world within 7 days.
2016 – VEEM Successfully lists on the Australian Stock Exchange
In October 2016, VEEM Ltd successfully listed on the ASX (code VEE).
2022 – VEEM manufactures components for Hawkei vehicles
VEEM Ltd began manufacturing and supplying ABT’s specialised park brake mechanism for Thales Australia’s Hawkei Protected Mobility Vehicle.
VEEM’s mark on history
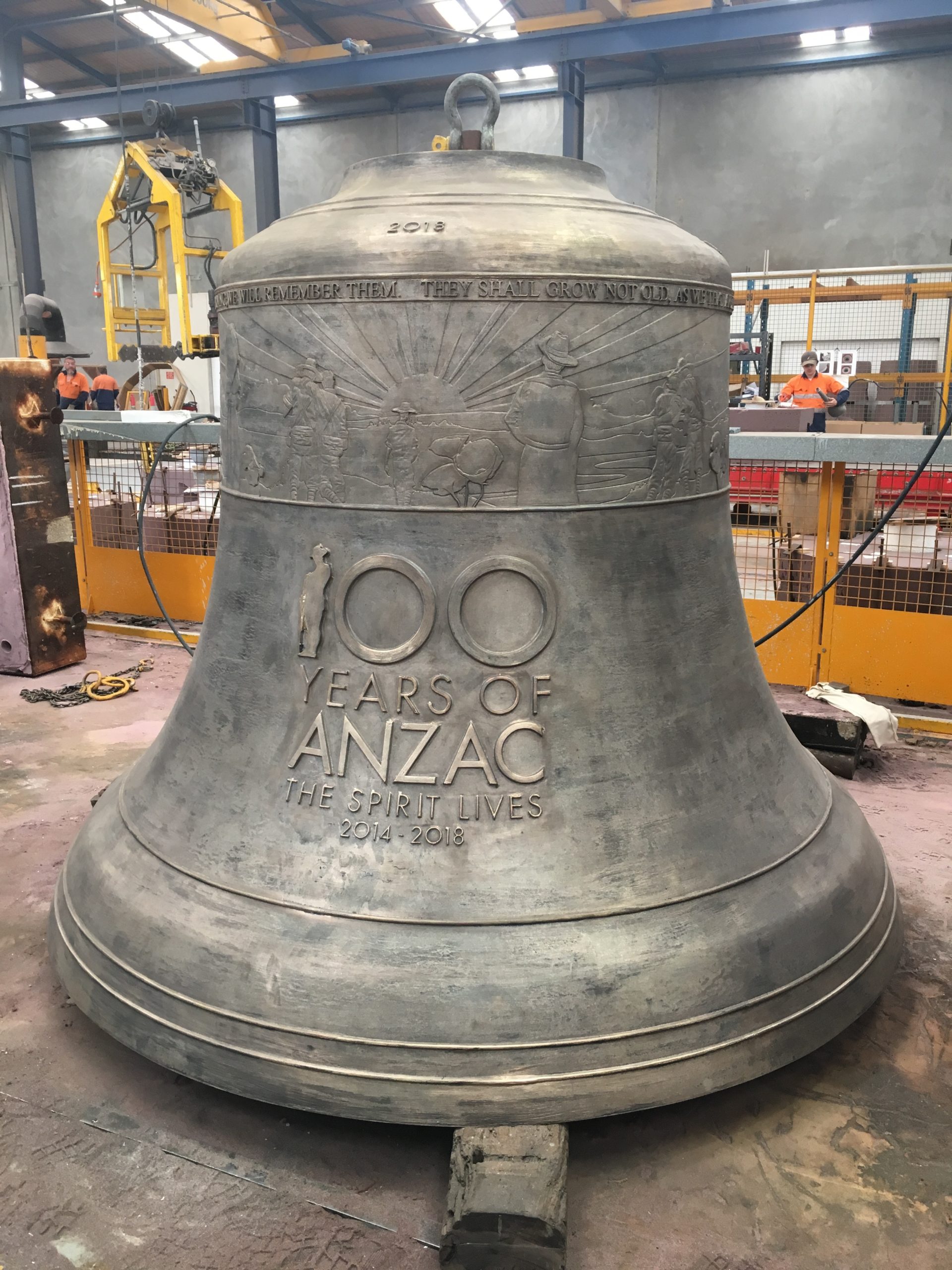
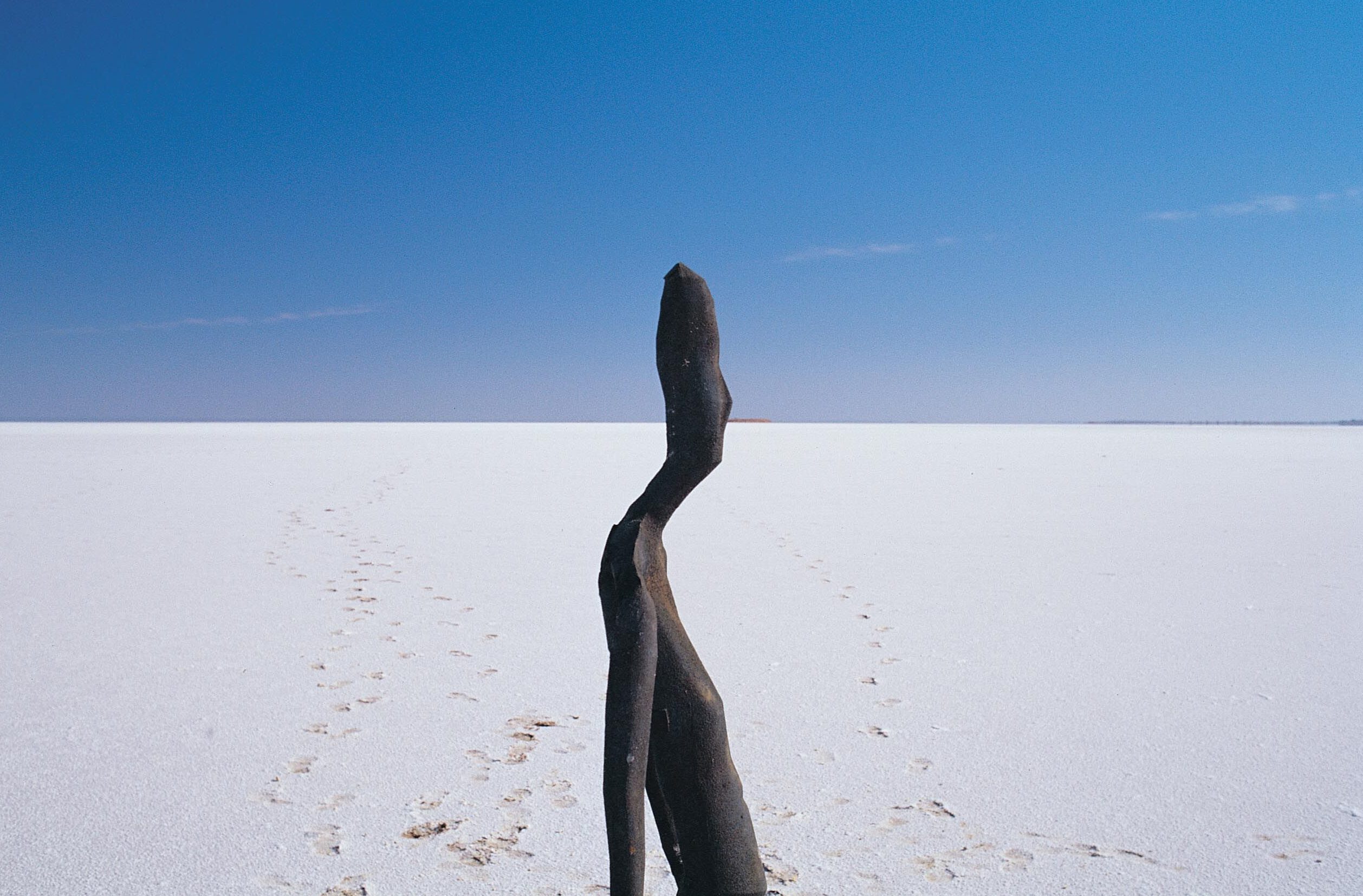
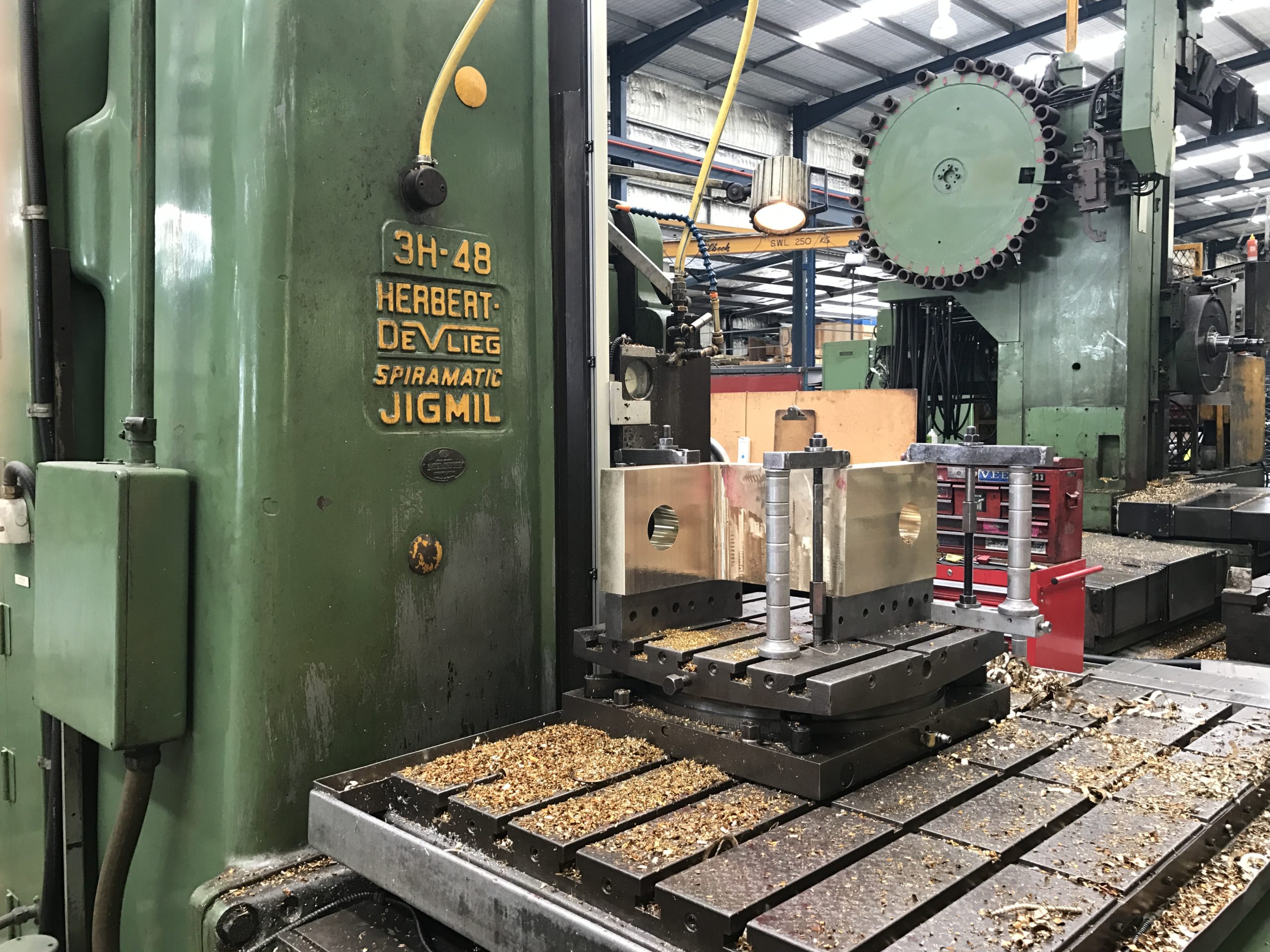
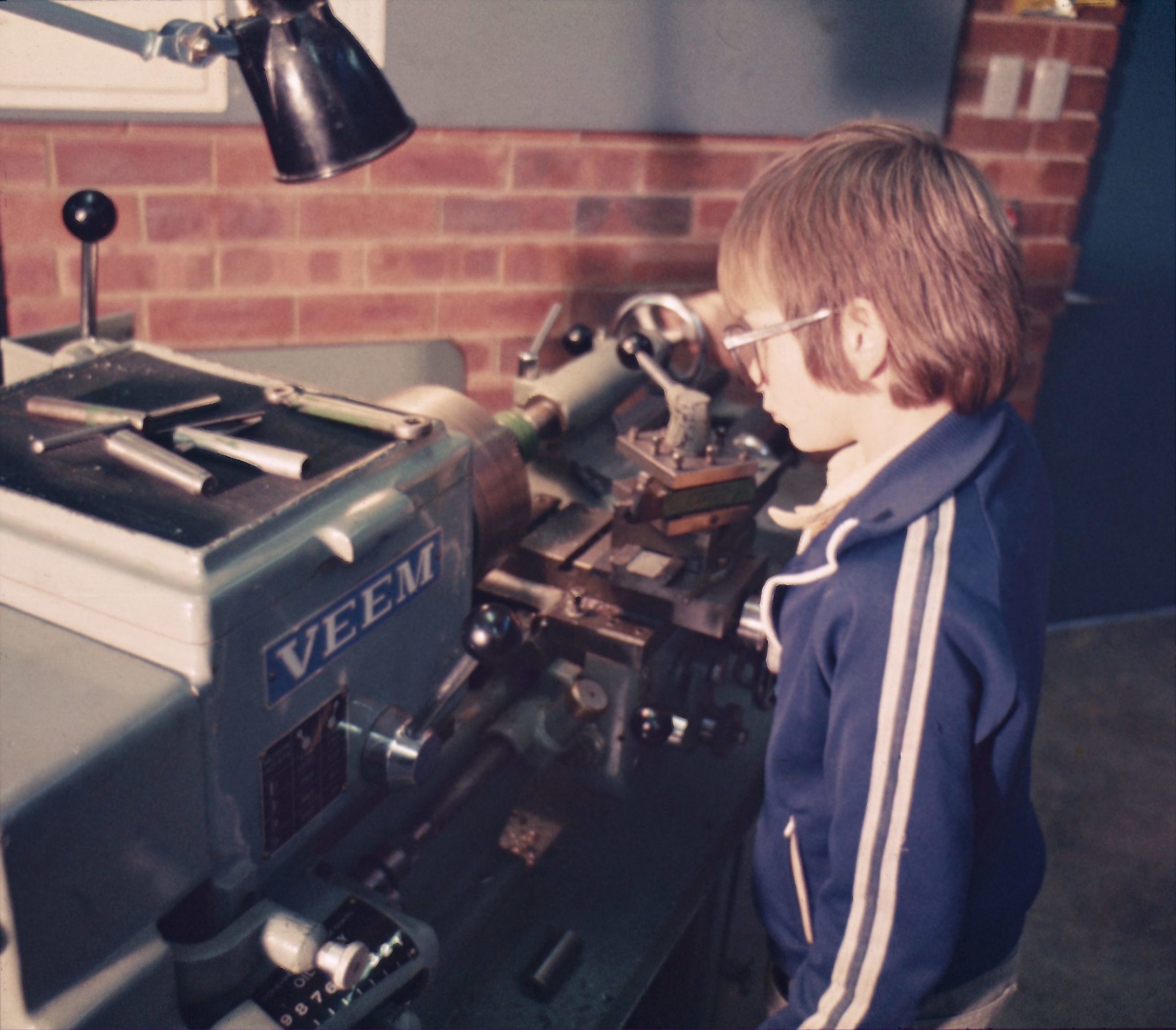
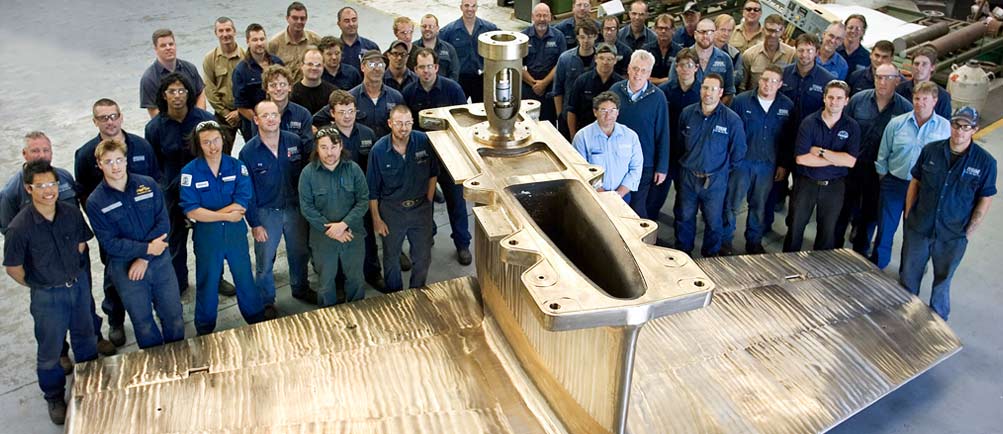
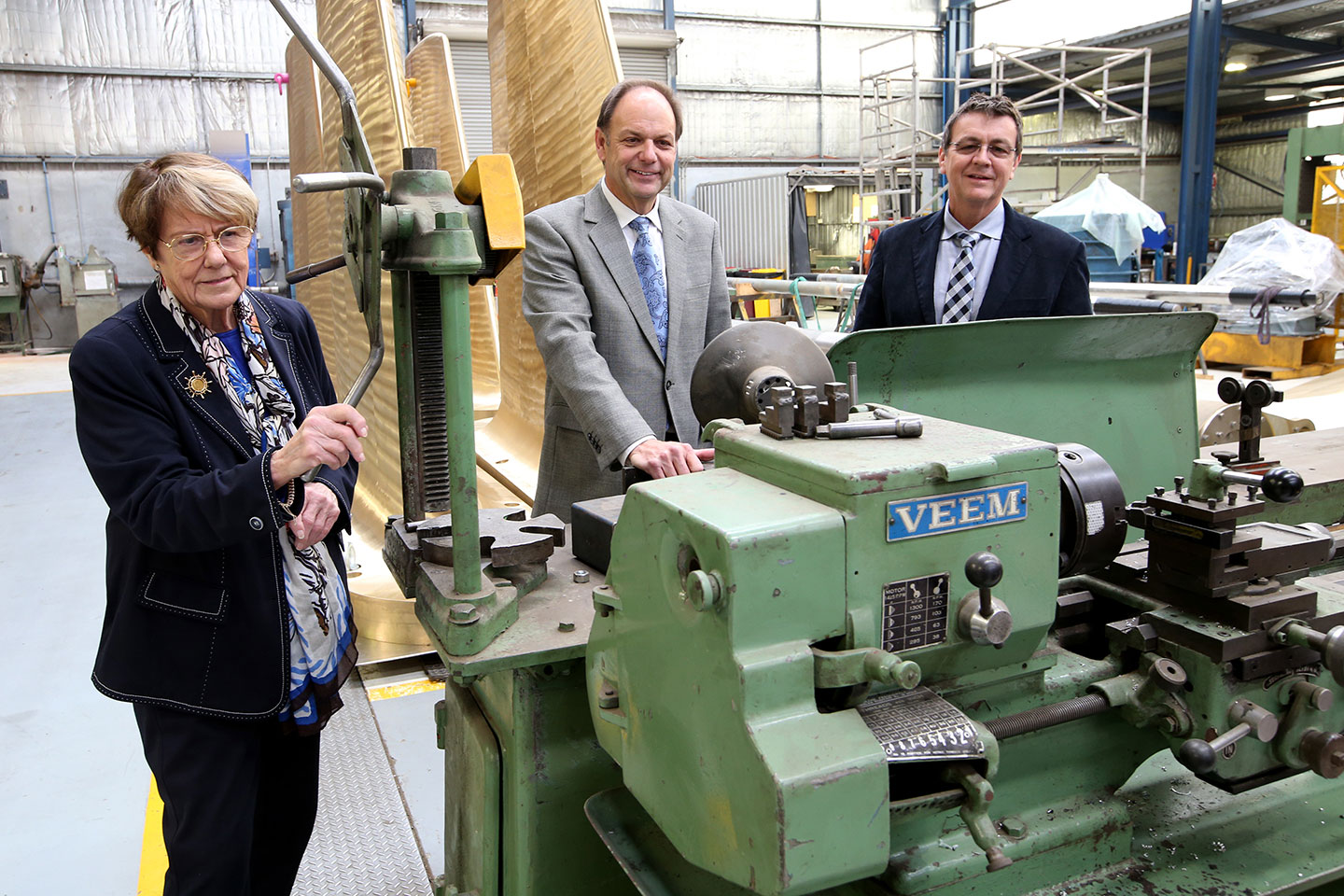
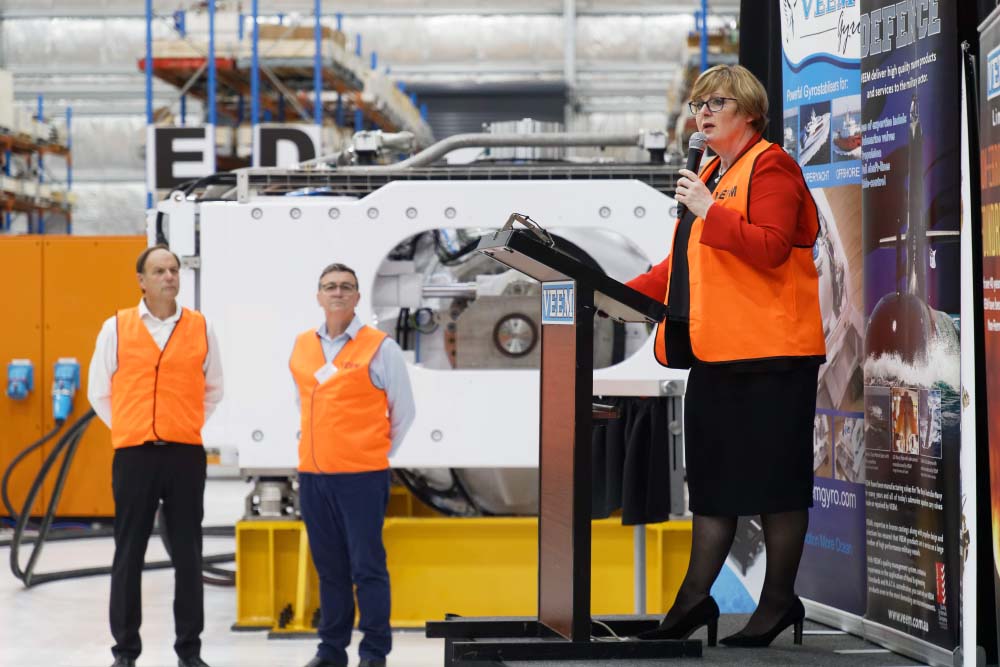
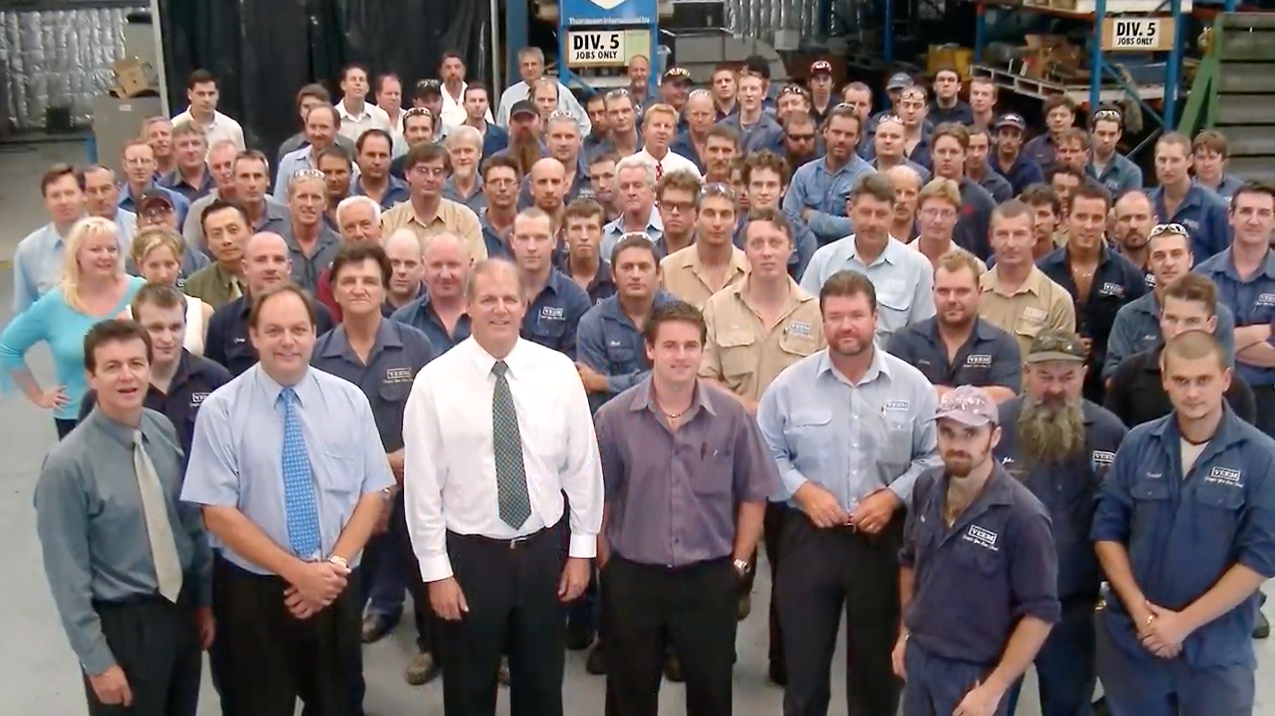
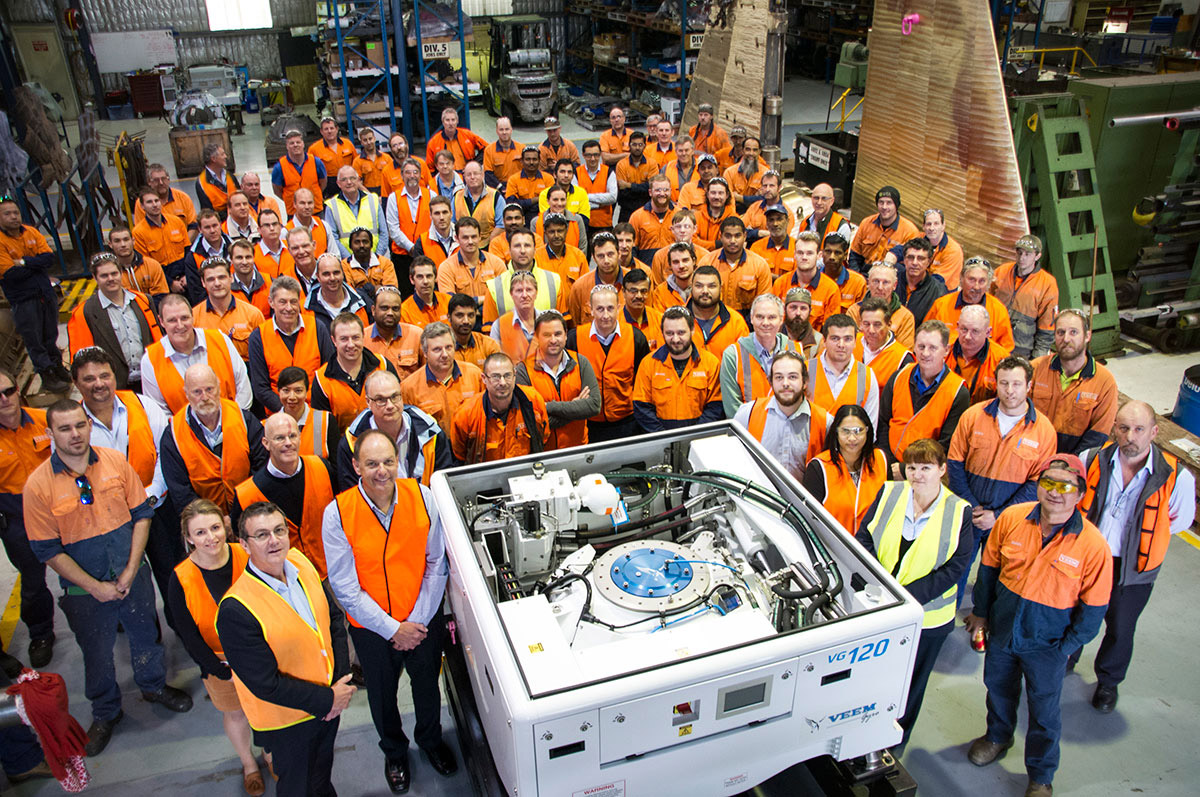